More than thirty percent of the manufactured clothes are never sold
It’s one of the first phrases I learned about the controversial textile market. Recently, Netflix released the fantastic documentary “Buy now!”, in which, in addition to stressing that “You’ve been played 100%. It’s a science, an intentional, complex and very refined science to get you to buy things,” it highlights that while companies like H&M or Zara create 25,000 and 36,000 new items a year, respectively, Shein launches 1,300,000.
Indeed, the problem in the textile industry is the same as in other areas: the excess of consumerism as a result of a process directed and planned by the brands (in the documentary mentioned above, it is also said, “We know you, we know your reaction to different messages because we have research departments dedicated to that“). In this context, accompanied by a good story or storytelling, we accepted the use of fragile phones with 5000 mah batteries when a decade ago, those same devices used replaceable 1000 mah batteries and were more resistant. Programmed obsolescence was accepted, as well as the design of products with an average life of two years, precisely the duration of the mandatory warranty. While the underlying problem is the same (that of prioritizing purely economic profit over anything else), the consequences in each product or market are different. We do not need so many products. Google, I’m only sometimes looking for something new. Please leave me alone and stop interrupting my videos with products I didn’t ask for and don’t want. And no, the most important things can’t be bought.
The textile industry's challenge: from environmental impact to a circular economy with recycled fibers
In the case of textiles, whose generated wealth accounts for 6 to 10% of the world’s annual wealth, the consequence is the excess of discarded products, such as the overexploitation of land or workers in developing countries. Yes, man is part of nature and the ecosystem. A large amount of clothing goes to secondary and low-cost markets, and when that route is finished, it is destroyed or sent to third countries to end up in a mountain of clothes in a distant city with an unpronounceable name.
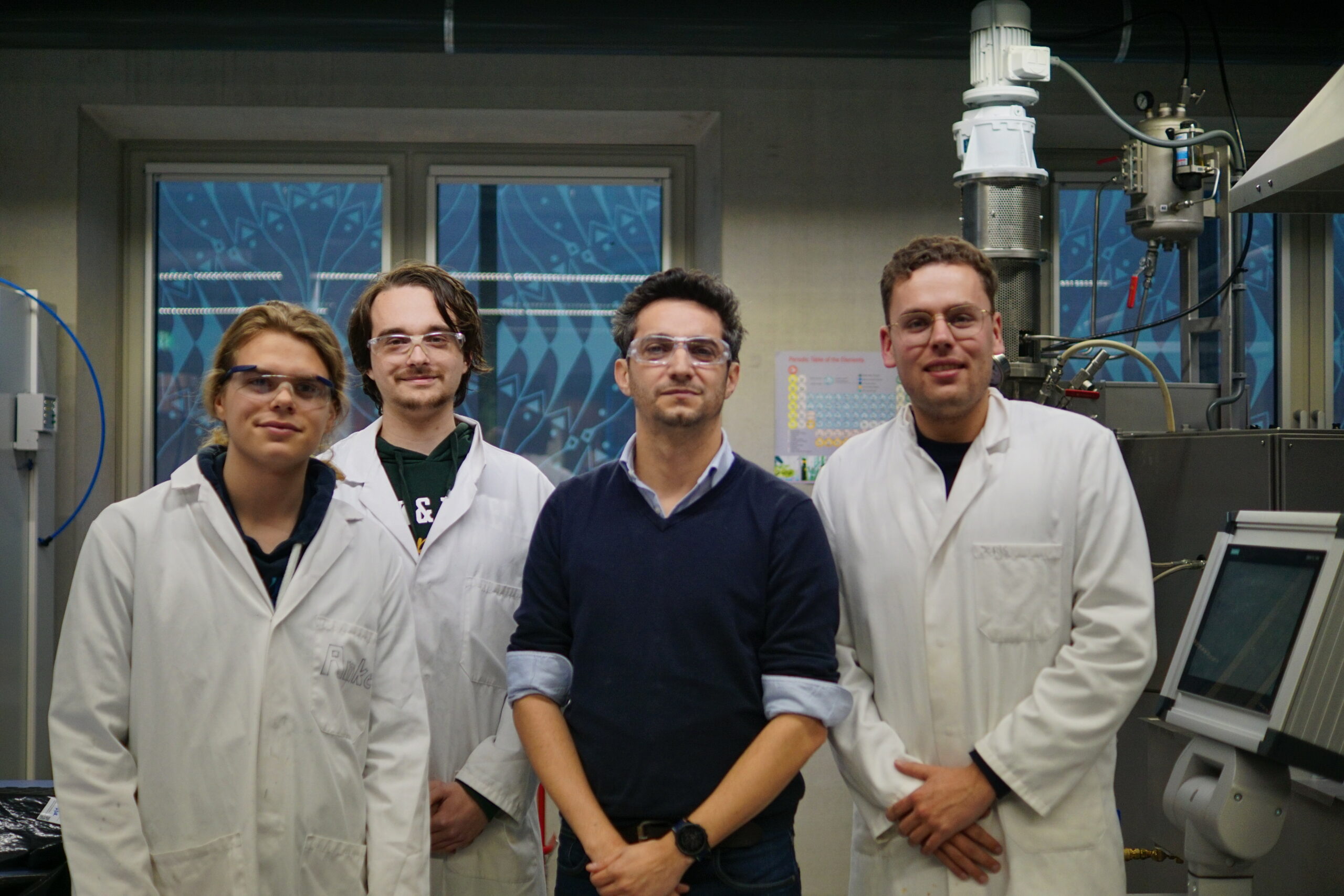
This would be enough to stop and review how we do things. In addition, polymers derived from petroleum, such as polyesters or polyamides (such as nylon or lycra), were introduced without considering their (excellent) mechanical properties as a fiber and their marketability performance. Every garment is degraded by the mechanical action of washing machines and the physico-chemical action of detergents. The result is that these polymers from oil end up in the sea. We have been doing this for decades, and although it could have been foreseen, we were surprised when we found microplastics in the ocean, in fish, and throughout the food chain, where they sometimes play a biological role that is far from innocent, such as acting as endocrine disruptors. This reality would not change if recycled plastics or other sources were used. As Churchill would say, we are now in a period of consequence.
In this context, recycling in general, and textile recycling in any of its aspects (mechanical or chemical) are only part of the solution. With regard to textile recycling, chemical recycling (which is complementary to mechanical recycling, not in competition with it) consists of obtaining the polymer in question from the discarded clothing. Therefore, at SaXcell (where I am CTO), we focus on textile recycling of the earth’s most abundant natural polymer, cellulose, in cotton. By extracting the polymer from discarded clothing and using appropriate treatment, we obtain a high-quality cellulose pulp ready for use in the Lyocell process to produce a cotton-like fiber. Lyocell is a process (established before SaXcell) that typically uses cellulose pulp from wood pulps, the origin of which is the felling of trees. Not only do we recycle the clothing, but we also avoid further tree felling along the way. In addition, the Lyocell process avoids using highly polluting chemicals as is the case to manufacture viscose, thus contributing to a sustainable industry. Hence, we choose to use our pulp in this technology. On the other hand, this type of chemical recycling is an alternative that can complement the more known and mature mechanical recycling, which has many technical limitations, low fiber quality, and loss of raw material in the process.
SAXCELL: Moving in the right direction
As of early 2024, SaXcell L30 fiber is available to fabric producers, with production currently running at 50 tons per month. Companies such as Bossa have used SaXcell for a denim collection recently presented at the Kingpin’s fair in Amsterdam.
In addition, a small production plant (3,000 tons per year) is planned in Enschede, in the Overijssel region, a research laboratory “Cellulose pulp development center” and a larger production plant in Turkey of 20,000 tons per year. Currently, SaXcell has two pilot plants (of two technologies to produce sustainable pulp) in our facilities. At the same time, the bulk of the production is done in India through our partner, Birla Cellulose. In Spain, companies such as Recover are dedicated to mechanical recycling, and in the future, Re&Up (part of the Sanko group) is considering building a plant in Spain.
This journey we undertook a few years ago with SaXcell will be full of challenges, but we will address them in due course. For the moment, we are taking steps in the right direction.
Can you help us to be more? Become a member and participate. Spread the word on the networks. Contact us and tell us about you and your project!
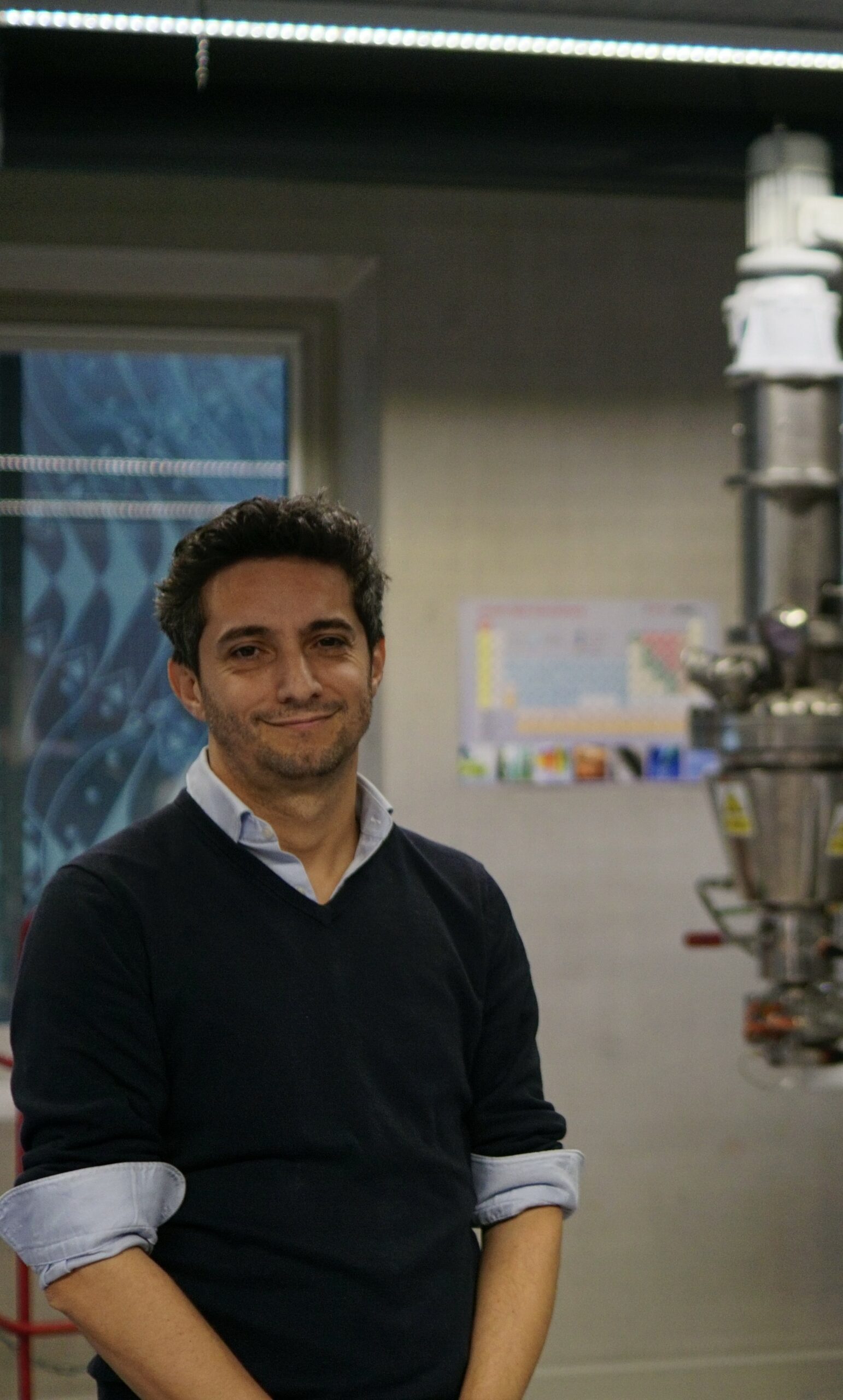
Antonio Martínez Pascual
CTO at SaXcell
Although my interest in science and technology has always been important to me, so has the responsibility that comes with creating something new and its possible impact on the environment and our society at all levels. That’s why my current interests also include philosophy and history, which teach us the limitations and mistakes of human beings. The more technified a society is, the more humanities are needed to navigate it.
I was born in the city of the largest Gothic Cathedral in the world. Every day, I wake up in Seville and have toast with olive oil and ham for breakfast. I also have a list of places I visit every time I return. I usually go to mass, take photographs in my free time, and play the occasional game of Play. But above all, what makes me happy is chatting with my goddaughter, Paulinita.